Reduce the Skills Gap : Skills Matrix
We’ve all heard the saying, “A picture is worth a thousand words,” but have you ever considered how it applies to your business?
Visual management boards are an essential lean manufacturing tool. They effectively communicate information at-a-glance to help coordinate and guide users towards continuous improvement. By developing a skills matrix board, everyone on the team can quickly identify strengths and potential skills gaps.
For clarification, according to Skills Base (https://www.skills-base.com), a digital skills inventory assessment company, “skills management is the practice of measuring and monitoring the skills of people within an organization, to develop workforce capability and align it with organizational objectives.”
In today’s changing and somewhat challenging work environment, cross-training capabilities are critical because there will be disruptions – it’s just a question of when. For Crafts Technology, embracing a visual skills matrix has been a powerful communication tool to assess, track, and report on skills, which has led to expected and unexpected continuous improvement throughout the organization.
Crafts conducts quarterly reviews where both the participant and manager evaluate an individual’s skills using an iPad multiple-choice assessment. Once both parties have completed the evaluation the numbers are averaged. Data compiled may identify areas that need work, uncover demonstratable competencies, or discover growth opportunities.
By embracing self-evaluation, there is a natural check and balance that helps provide a more effective assessment by focusing on gaining agreement. When using a skills matrix, the focus is on the skill and not necessarily directed to the person, which reduces opinion bias and improves open dialogue. See the below table for rankings used by Crafts.
Crafts Technology |
0. Not Applicable: No working knowledge of the process or operation. |
1. Low Skill: Minimal understanding of the process or operation. Capable of performing the operation with heavy guidance from individuals with a higher skill level. Does understand safety and quality compliance of the process or operation. |
2. Basic Skill: Basic understanding of the process or operation. Capable of performing the operation somewhat independently, with some higher skill level guidance. Does understands safety and quality compliance of the process or operation. |
3. Competent Skill: Competent understanding of the process or operation. Capable of performing the operation independently, with minimal higher skill level guidance. Does understands safety and quality compliance of the process or operation. |
4. Developed Skill: Developed understanding of the process or operation. Capable of performing the operation independently. Is capable of training lower skill level individuals. Does understands safety and quality compliance of the process or operation. |
At Crafts Technology, the skills matrix is the foundation of human resources’ continuous improvement initiative. Participants include operations, engineering, and leadership who are assessed on both soft and hard skills. The skills matrix board visually showcases information in one location, allowing everyone to work from the same perspective, which aids in setting goals and motivates team members to learn new skills.
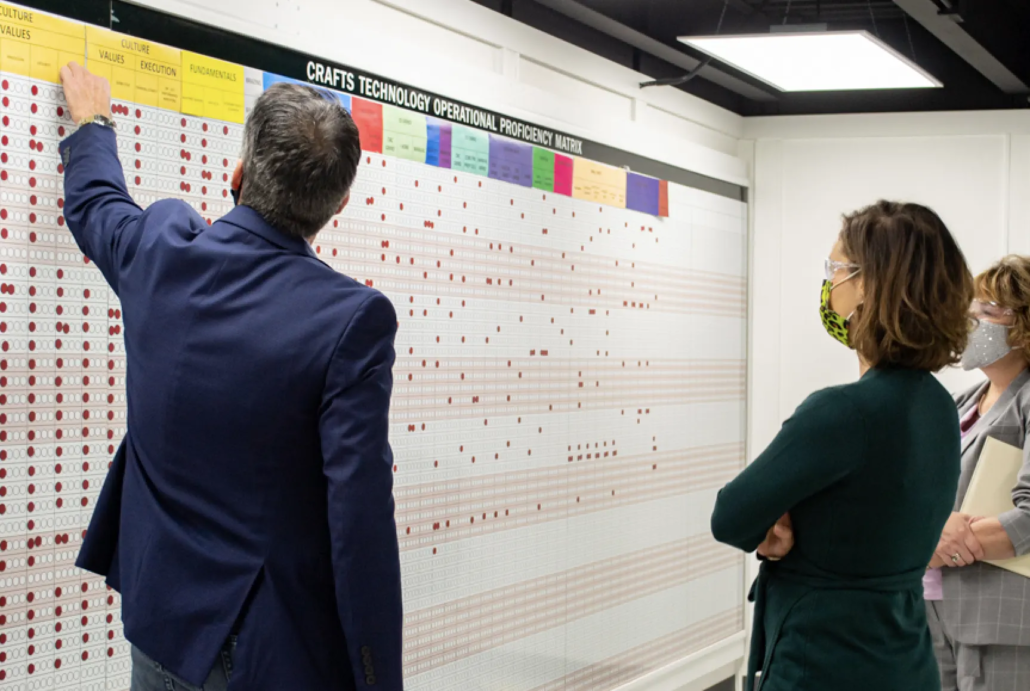
Since implementing a skills matrix board, Crafts Technology has experienced several positive changes:
- Identified the mismatch between the required skills and the skills that are possessed by team members
- Encouraged cross-training to develop a more flexible workforce that can adjust to spikes in demand or COVID related absences
- Improved employees’ motivation to learn new skills because everyone better understands the expectations
- Mitigated risk by allowing a backup system to surface so that roles can be filled when people are off, particularly in today’s COVID-19 environment
- Increased company growth by improving communication and skills throughout the organization
- Reduced the skills gaps by highlighting training opportunities
- Improved retention rates by better utilization employee strengths and offering training to address weaknesses
- Enhanced employee satisfaction by transparently sharing information and empowering each team member
By using skills matrix software, Crafts Technology has aggregated data that provides insights that far exceed Excel or other collection methods, which has been instrumental in setting company goals. As a company, Crafts is committed to continuous improvement – as individuals’ skills shouldn’t be static. By mapping skills across the organization Crafts can predict, adapt, and respond proactively to issues.
Jeffrey Roberts, Vice President of Engineering at Crafts Technology, reports, “At Crafts the skills matrix is an important lean management tool that helps us reach our goal of continuous improvement and best in class. It’s proven especially useful when evaluating our skills gap. We’ve used it to enhance cross-training and found it motivates all involved.”
By using visual management boards like a skills matrix, Crafts Technology provides a stronger message than words alone, which has enabled them to effectively maximize their entire team’s skills.